Causes of damage to ladle purging plug
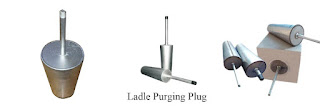
1. Thermal stress The ladle purging plug directly contacts the high-temperature molten steel, and is subject to the continuous cold air flow, which generates a large temperature gradient, resulting in high concentration of stress. 2.Scour and abrasion The blown gas gives a certain reverse impact force to the working surface of the purging plug , and at the same time has a shearing and scouring effect on the purging plug. 3.Chemical erosion The material of the purging plug reacts with the molten steel penetrating the slit and the slag that has eroded into the working layer, which changes the physical and chemical properties of the working layer of the purging plug and increases the tendency of spalling. 4.Burning oxygen cleaning The high temperature when burning oxygen is very fatal to ladle purging plug , and the melt loss within a few minutes is many times higher than the normal refining erosion. Wanhao is a manufacturer who is specialized in designing various k...