Construction spraying method of refractory spray coating
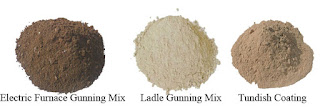
The spraying methods of refractory spray coatings are divided into three types: wet method, dry method and flame method. 1.Wet spraying refers to the spray surface of refractory spray coating after adding water or liquid binder. Wet spraying is divided into four types: mud method, wet method, semi-dry method and pseudo-dry method. The mud method is to mix the refractory mixture into a slurry before spraying, and is mainly used for thermal gunning of furnace lining ; the wet method is to stir the refractory mixture into pumping mud and then spray; the semi-dry method is to add the refractory mixture first A small amount of water is stirred evenly. When it is delivered to the nozzle, the remaining water is added and then sprayed; the false dry method is to stir the refractory mixture evenly through a mixer, and then send it to the nozzle to add water for spraying. 2. Dry spraying means to spray the mixed refractory spray coating directly to the sprayed surface through the